

CALL OR EMAIL US NOW!

In May 2015, SMARTHEAD LLC was formed to solve the "late hollow metal delivery" problem that has plagued contractors in our industry for over half a century. The reasons for delayed delivery is well‐known ‐ the shop drawing approval process, the fact that fabrication can’t start until final hardware decisions are made, revised schedules, etc. These factors can create conflict, inefficiency, frustration and COSTS to the trades affected. As the door/buck/hardware package becomes more and more complex, this problem becomes more prevalent. A current trend by GCs and CMs to include the furnishing of hollow metal in the carpentry package is added incentive for carpentry contractors to use the SMARTHEAD to maintain workflow and productivity. After some brainstorming, a prototype was created. It was then reviewed by a group of industry professionals ‐ GCs, carpentry contractors, electrical contractors - some tweaking of dimensions and details ensued. The initial proof‐of‐ concept opportunity came quickly in July 2015 when 50 SMARTHEAD units were sent to a hospital project in NYC. After installation of the SMARTHEAD, our carpentry contractor was able to complete all framing, 95% of insulation, drywall, fascia & soffits, spackling and acoustical ceilings. ALL this was done prior to the delivery of hollow metal frames. The hollow metal was received on Aug 13th; by the end of the week all hollow metal, sheetrock rips and tape & spackle was complete. By 2016, five hundred SMARTHEAD units were installed on 20+ projects including School Construction Authority (SCA) jobs, hospitals, retail, high rise and administrative offices. We have thoroughly vetted SMARTHEAD, proven the concept and are currently releasing this product to the industry.
For additional product information, visit us at www.smartheadsolution.com, email us at sales@duraframesolutions.com or call us at


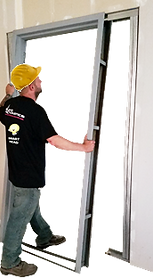

